Korozja metali - sposoby jej zapobiegania
ROZDZIAŁ II - PODSTAWY TECHNIKI część VII (str. 25-29) Aleksander Lisowski Wyd. "Hortpress"
Korozja jest zjawiskiem, które stopniowo niszczy, pod wpływem chemicznego i elektrochemicznego oddziaływania środowiska, wszystkie tworzywa i materiały stosowane w technice, począwszy od metali, poprzez betony, żelbetony, ceramikę, drewno - do tworzyw sztucznych włącznie. Ogólnie korozja jest to nieodwracalna reakcja materiału z otoczeniem. Korozja w największym stopniu odnosi się do metali i ich stopów materiałów konstrukcyjnych pojazdów i maszyn rolniczych, które są użytkowane w naturalnym środowisku zawierającym zanieczyszczenia chemiczne. Oddziaływanie chemiczne i elektrochemiczne w połączeniu z wilgotnym powietrzem (powyżej 70%) przyspiesza proces łączenia żelaza z tlenem i wodorem i utworzenia się rdzy. Ten rodzaj korozji, zachodzący w środowisku naturalnym, nazywa się korozją atmosferyczną i stanowi największy problem dla użytkowników sprzętu rolniczego. Groźne są również korozja międzykrystaliczna i wżerowa, które są niewidoczne, a powodują bardzo poważne zmniejszenie wytrzymałości części maszyn.
Korozja rozpoczyna się zwykle drobnymi zmianami zaatakowanej zewnętrznej powierzchni, występującymi najczęściej w miejscach zagięcia materiału, a następnie postępuje wgłąb, niszcząc jego najbardziej podatną strukturę, co wpływa silnie na zmniejszenie wytrzymałości zarówno materiału, jak i konstrukcji.
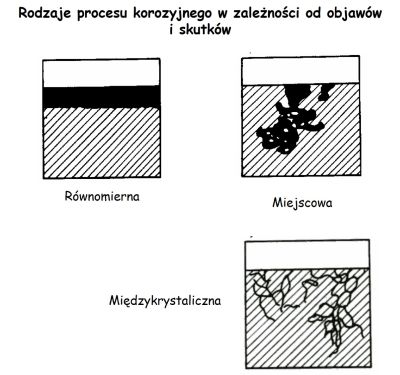
Aby skutecznie przeciwdziałać korozji, należy wiedzieć, że mechanizm jej powstawania może być chemiczny (np. w suchych gazach lub cieczach nieprzewodzących prądu elektrycznego) lub - częściej - elektrochemiczny. Korozja tego ostatniego typu zachodzi nie tylko w atmosferze, ale także w środowiskach ciekłych, wodnych roztworach i wilgotnych glebach, a więc w środowisku pracy sprzętu rolniczego. Korozja elektrochemiczna powstaje wskutek reakcji krótko zwartych ogniw na styku metalu z elektrolitem (np. znajdującym się w wilgotnej glebie). Ogniwa te powstają w rezultacie niejednorodności chemicznej (lub fizycznej) metalu, np. na styku różnych metali, bądź wskutek niejednorodności krystalicznej w strukturze metalu. utworzone mikro-ogniwa wyzwalają procesy galwanizacji rozpuszczające metal i w końcowej fazie wodorotlenek żelaza utlenia się na powietrzu i powstaje rdza, będąca mieszaniną uwodnionych tlenków żelaza, która ułatwia dalszy postęp korozji. Na niektórych metalach produkty korozji tworzą czasami warstwę pasywną, chroniącą przed dalszym rozkładem (miedź, srebro).
Z mechanizmu powstawania korozji wynika, że czynnikami ją przyspieszającymi są niekorzystne właściwości metalu (zanieczyszczenia pierwiastkami o większym potencjale elektrochemicznym, nieprawidłowy sposób obróbki), trudne warunki pracy sprzętu rolniczego (tarcie, obciążenia zmienne elementów roboczych o różnym kształcie), bardziej kwaśne środowisko (dwutlenek węgla w powietrzu, siarka, kwaśna gleba), podwyższona temperatura, długotrwałe użytkowanie sprzętu rolniczego, kontakt stali z mniej aktywnym materiałem (w powstałym ogniwie mniej aktywny metal pełni rolę katody, czyli rolę elektrody redukcji przyłączania się jonów). Wynika z tego, że powłoki ochronne w postaci warstwy cynku, miedzi lub niklu są skuteczne do chwili, gdy są szczelne. Z chwilą jej uszkodzenia w obecności wilgoci i zanieczyszczeń korozja stali zachodzi intensywniej niż bez takiej powłoki.
Powstający produkt korozji - rdza, która tworzy się z metalu, powoduje jego ubytek zmniejszenie przekroju części, co wpływa na obniżenie trwałość elementów konstrukcyjnych sprzętu rolniczego. Zmniejsza się wytrzymałość części, które szybciej się zużywają oraz łatwiej i częściej ulegają uszkodzeniom, a sprzęt rolniczy jest mniej niezawodny, gdyż podlega większej liczbie awarii i przestojów. Zwiększa to koszty eksploatacji, wydłuża wykonanie prac w zaplanowanym, optymalnym okresie agrotechnicznym. Dodatkowo zwiększa to straty wynikające z nieterminowego ich przeprowadzenia (np. opóźnienie zbioru zbóż przyczynia się do zwiększenia strat ziarna w wyniku jego osypywania się lub porośnięcia - przy niesprzyjającej pogodzie). Czas użytkowania takiego sprzętu rolniczego jest również krótszy, co zwiększa koszty jednostkowe jego eksploatacji. Skorodowane powierzchnie robocze elementów pracujących w glebie zwiększają opory, na których pokonanie ciągnik zużywa więcej paliwa. Skorodowane elementy robocze działają gorzej, co wpływa na pogorszenie ich jakość pracy. Dotyczy to nie tylko elementów pracujących w glebie, ale także elementów rozsiewaczy nawozów, opryskiwaczy, deszczowni i urządzeń pracujących w pomieszczeniach inwentarskich.
1.7.Sposoby zabezpieczania metali i ich stopów przed korozjąOchrona części i maszyn przed korozją może być trwała lub czasowa.
Trwałą ochronę części sprzętu rolniczego przed korozją planuje się na etapie projektowania konstrukcji maszyn, ich produkcji i napraw głównych. Do trwałych sposobów ochrony korozyjnej należą procesy chemicznej obróbki powierzchni metali: oksydowanie, fosfatowanie (dotyczy odtłuszczenia) lub powlekanie farbą przeciwkorozyjną czy też galwaniczne pokrywanie metaliczną powłoką. Bardzo dobre efekty uzyskuje się przez zastosowanie kataforezy techniki nakładania powłok malarskich wykorzystującą zjawisko elektroforezy, to jest rozdzielania substancji chemicznych pod wpływem pola elektrycznego.
Ochrona czasowa przed korozją pozwala na okresowe zablokowanie lub znaczne zmniejszenie wpływu środowiska korodującego. Stosowana jest na czas transportu, przechowywania i użytkowania sprzętu rolniczego, ale także w okresie obróbki i montażu. Podstawowe sposoby stałej (trwałej) ochrony przeciw korozji i rdzewieniu metali to:
- dobór odpowiedniego metalu, w zależności od właściwości (agresywności) środowiska;
- modyfikacja składu pierwiastkowego metalu przez wprowadzanie domieszek metali lub innych pierwiastków powodujących lepszą odporność na korozję;
- nanoszenie na powierzchnię metalu metalicznych powłok ochronnych, odpornych na korozję (niklowanie, chromowanie, złocenie itp.);
- nanoszenie niemetalicznych powłok ochronnych odpornych na korozję (lakierowanie, emaliowanie, cementowanie oraz nakładanie: asfaltu, smoły, parafiny, smarów plastycznych, olejów itp.);
- zmiana struktury powierzchni metalu lub składu chemicznego warstwy powierzchniowej przez wytworzenie na jego powierzchni związku chemicznego (najczęściej tlenku, fosforanu chromianu itp.) w wyniku zabiegów chemicznych lub elektrochemicznych ( nawęglanie, oksydowanie, utlenianie anodowe, fosforanowanie, chromianowanie, pasywacja itp.);
- ochrona katodowa (anodowa) polegająca na tym, że do chronionej konstrukcji dołącza się zewnętrzną anodę (katodę) w postaci metalu o potencjale elektrodowym niższym (wyższym) niż metal, z którego jest wykonana chroniona konstrukcja (np. cynk w przypadku katodowej ochrony urządzeń wykonanych ze stali);- stosowanie inhibitorów korozji (środków hamujących korozję) w składzie środka agresywnego, a także w składzie środków smarnych, paliw, cieczy eksploatacyjnych, cieczy do obróbki metali, gazów;
- osłabianie agresywności środowiska, np. przez osuszanie powietrza
Ponieważ przy usuwaniu pokryć ochronnych istnieje niebezpieczeństwo naruszenia powierzchni materiału, dlatego aby uniknąć tych wad, stosuje się czasową ochronę przed korozją. Polega ona na konserwacji sprzętu rolniczego łatwo usuwalnymi lub niewymagającymi usuwania środkami konserwacyjnymi oraz na pakowaniu ochronnym (zwłaszcza części).
Środki czasowej ochrony przed korozją są to substancje nakładane na powierzchnie metalowe lub powłoki ochronne niemetaliczne, tworzące na powierzchni łatwousuwalne lub niewymagające usuwania powłoki, chroniące metal przed korozją w określonym środowisku i ograniczonym czasie.
Do środków ochrony czasowej metali przed korozją zaliczamy:- oleje mineralne z pakietem dodatków - oleje konserwacyjne;
- oleje konserwacyjne z rozpuszczalnikiem;
- smary węglowodorowe lub zawierające zagęszczacz mydlany z pakietem dodatków - smary konserwacyjne;
- smary konserwacyjne z rozpuszczalnikiem;
- roztwory wosków lub lanoliny z pakietem dodatków;
- substancje syntetyczne tworzące cienki lub ultracienki film, będący zazwyczaj specjalnym Inhibitorem korozji z dodatkiem rozpuszczalnika;
- wodne emulsje zawierające środek konserwacyjny;
Środki ochrony czasowej zawierają także dodatki: inhibitory utlenienia, substancje zwilżające , biocydy (środki syntetyczne przeciwdziałające rozwojowi mikroorganizmów), barwniki, smary konserwacyjne, a także zagęszczacze.
Środki ochrony czasowej są klasyfikowane z uwzględnieniem czasu ochrony, konsystencji i składu chemicznego oraz innych kryteriów zawartych w przedmiotowych normach krajowych i międzynarodowych.
Środki ochrony czasowej można nanosić przez- zanurzenie detalu;
- natrysk na powierzchnię;
- malowanie pędzlem (smarowanie).
W razie konieczności środki ochrony czasowej można usunąć:
- mechanicznie - złuszczając je, ścierając lub skrobiąc;
- myjąc rozpuszczalnikami organicznymi - na zimno lub na gorąco
- myjąc wodnymi roztworami detergentów - na zimno lub na gorąco;
- działając gorącą parą wodną pod niskim ciśnieniem.
W ofercie handlowej znajduje się wiele różnorodnych środków ochrony przed korozją. Niektóre z nich trzeba przygotowywać samemu bezpośrednio przed ich zastosowaniem, ale jest wiele gotowych preparatów. Do takich zalicza się inhibitory korozji, które mogą być lotne lub nielotne.
Z oferty handlowej środków ochrony przed korozją można wymienić m.in.:
- Antykor - inhibitor korozji
- Akorin - (smar) przekładnie zębate otwarte, łańcuchowe, przeguby, śruby regulacyjne, wielowypusty;
- Antykol - olej ochronny do precyzyjnych wyrobów metalowych, części silników spalinowych;
- Fluidol - (płyn) wszystkie metale ze względu na brak aktywności chemicznej;
- Elektrosol - (płyn) do ochrony elementów stykowych w układach elektrycznych;
- Agrokor - emulsja wodno-woskowa do sprzętu rolniczego przechowywanego na wolnym powietrzu;
- Bitex, Protektol, Karplast - do podwozi pojazdów i konstrukcji metalowych;
- Cortanin, Kompleksor - środki przetwarzające produkty korozji, wchodzą w reakcję z rdzą i ją stabilizują.
Niektóre nowoczesne farby, emalie i lakiery, zaliczane do środków ochrony przed korozją, możemy bezpośrednio nakładać na powierzchnie skorodowane, gdyż zawierają substancje czynne, które wiążą produkty korozji. Lepsze efekty uzyskuje się jednak po starannym przygotowaniu powierzchni metalowych przed nałożeniem powłok antykorozyjnych. Polega to na usunięciu resztek łuszczącej się powłoki ochronnej i luźnych produktów korozji oraz oszlifowaniu części, aż do uzyskania czystej powierzchni metalu, wolnej od korozji. Do nakładania środków płynnych możemy zastosować pędzle lub pistolety natryskowe. Niektóre środki mają postać aerozolu, co znacznie ułatwia wykonanie prac.
Przed przystąpieniem do nałożenia środków ochrony przeciw korozji, należy zapoznać się z instrukcją obsługi zamieszczoną na opakowaniu danego środka, i bezwzględnie przestrzegać zasad w niej zawartych, zwłaszcza wówczas, gdy używamy środków niebezpiecznych.